Plasma cutting technology is widely employed in steel and metal cutting operations, particularly when combined with CNC plasma arc cutting. Are you familiar with this cutting method? Moreover, how does it compare to other metal cutting techniques?
In the forthcoming articles, we'll provide comprehensive tips and guidance on plasma cutting services, ensuring you have all the information you need.
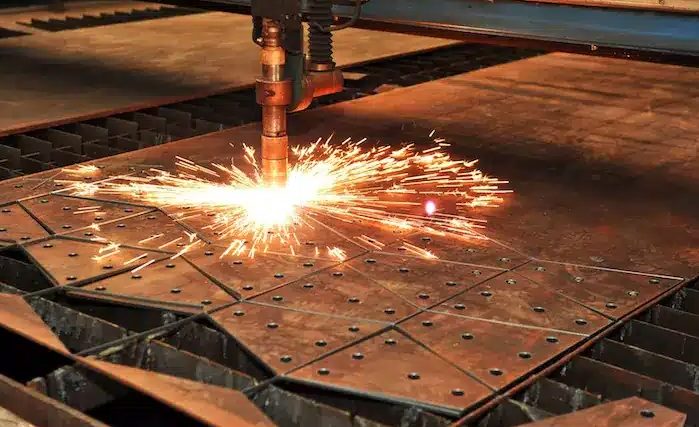
What is Plasma Cutting?
Plasma cutting utilizes the intense heat generated from a high-temperature plasma electric arc to sever steel components. During the cutting process, metal materials are melted and vaporized, with plasma power employed to remove the resulting metal fusion.
The history of plasma arc cutting technology traces back to the 1960s, evolving from plasma welding techniques. By the 1980s, it emerged as a highly efficient method for cutting sheet and plate metal. Plasma cutting offered significant advantages over conventional "metal against metal" cutting, including the elimination of metal clippings, precise cuts, and the creation of refined edges compared to oxy-fuel slicing. Initially, plasma cutters were large, relatively slow, and costly, primarily suited for repetitive cutting tasks in mass production scenarios.
Plasma cutting is proficient in slicing through electrically conductive materials by utilizing an accelerated stream of hot plasma. It is capable of cutting various materials, including different types of steels. Common materials processed with a plasma torch encompass carbon steel, alloy steel, stainless steel, aluminum, brass, and copper, although it can also handle various other conductive metals.
What it is used for?
Plasma cutting finds widespread application across various sectors including automotive repair and restoration, manufacturing facilities, salvage yards, and industrial construction. Its ability to deliver swift and precise cuts at a relatively low cost makes it suitable for a broad spectrum of users, ranging from large-scale industrial CNC operations to small hobbyist workshops.
Plasma Cutting Overview and Techniques The fundamental process of plasma cutting involves generating an electrically ionized gas plasma channel from the plasma cutting device, passing it through the material to be cut, and completing an electric circuit back to the plasma cutter via a grounding clamp.
This process utilizes pressurized gas (such as oxygen, air, or inert gases depending on the material being cut), expelled at high velocity through a concentrated nozzle towards the workpiece. An electric arc forms within the gas, between an electrode near or within the gas nozzle and the workpiece. The electric arc ionizes a portion of the gas, creating a conductive plasma channel. Simultaneously, the high-speed plasma and pressurized gas expel the molten metal, effectively slicing through the material.
Versatile Cutting Option for Thin and Thick Steel Plates Plasma cutting offers an efficient means of cutting both thin and thick steel plates, as well as other metal materials. Hand-held torches can cut steel plates up to 38 mm (1.5 in) thick, while more powerful computer-controlled torches can slice steel up to 150 mm (6 in) thick. The capability of plasma cutters to generate a highly focused and intense "cone" enables cutting of metal sheets with intricate shapes and profiles, including rounded or angled designs.
How CNC (computer numerical control) integrated in Plasma Cutting
Like many other types of machinery, CNC (computer numerical control) technology was integrated into plasma cutting equipment in the late 1980s and throughout the 1990s. This advancement provided plasma cutting devices with enhanced versatility, enabling them to cut a wide range of designs "on demand" based on specific instructions programmed into the machine's numerical control system.
Initially, CNC plasma cutting machines were primarily used for cutting designs and components in flat steel sheets, utilizing only two axes of movement (referred to as X Y cutting).
Starting methods for plasma cutting tools vary. Some machines create the arc by establishing contact between the torch and the material being cut, while others use high voltage and high-frequency electrical connections to initiate the arc. However, these methods have drawbacks such as the risk of electric shocks, maintenance issues, and high levels of radio frequency emissions. Plasma cutting tools used near sensitive electronic equipment, like CNC machinery or computers, employ alternative methods to initiate the pilot arc, such as contact between the nozzle and the electrode.
Several manufacturers produce CNC cutting tables specifically designed for plasma cutting, while others integrate the cutter directly into the cutting table. CNC tables allow a computer to control the torch head, ensuring precise and clean cuts.
Modern CNC plasma equipment can cut thick materials on multiple axes, enabling the creation of complex welding joints that were previously impossible with other methods. However, for thinner metals, laser cutting is gradually replacing plasma cutting due to its superior hole-cutting capabilities.
One notable application of CNC Plasma Cutters is in the HVAC field, where software analyzes ductwork details and generates flat patterns to be cut on the cutting table using a plasma torch. This technology has significantly improved efficiency in the sector since its introduction in the early 1980s.
CNC Plasma Cutting services are also utilized in various workshops to create intricate metalwork, including commercial and residential signs, wall art, designs, street address signs, and exterior garden art.
In recent years, vertical CNC plasma cutting devices have become available, offering a compact footprint, increased flexibility, improved safety, and faster performance compared to traditional horizontal cutting tables.
CNC Plasma Cutting is available in three main configurations, primarily distinguished by the types of materials processed and the flexibility of the cutting head:
a. 2 Axis Plasma Cutting (2D):This is the conventional and widely used form of CNC Plasma Cutting. It generates flat profiles with cut edges at a 90-degree angle to the material surface. CNC Plasma Cutting beds configured in this manner, especially those with high power, can cut profiles from metal plates ranging from 30mm to 150mm thick.
b. 3 Axis Plasma Cutting (3D):Similar to 2D cutting, this method creates flat profiles from thin steel plates or sheet metal. However, with the addition of an extra rotational axis, the cutting head of the CNC Plasma Cutting machine can tilt while following a standard 2-dimensional cutting path. This results in cut edges at angles other than 90 degrees to the material surface, typically ranging from 30 to 45 degrees.
The consistent angle across the material thickness is often used in applications where the profile will be welded, as the edge angle contributes to the weld preparation. This integration of weld preparation during the CNC plasma cutting process can eliminate the need for additional operations such as milling or machining, thus reducing costs. Additionally, the angular cutting capability of 3D plasma cutting can be utilized to create countersunk holes and chamfer edges of profiled holes.
c. Steel Pipe and Tube Plasma Cutting:This method is employed for processing tubes, pipes, or any elongated sections such as H beams, C beams, or L steel profiles. During the cutting process, the plasma cutting torch remains stationary while the workpiece is fed through and rotated around its longitudinal axis.
In certain setups, similar to 3D Plasma Cutting, the cutting torch can also pivot and rotate, enabling angled cuts throughout the thickness of the section or tube. This capability is commonly used in the fabrication of process pipework, where cut pipes can be supplied with weld preparations instead of straight edges.
How will Plasma Cutting Technology evolve to enhance performance?
To achieve superior cutting precision, recent advancements in plasma torch design have yielded a sleeker nozzle and a narrower plasma arc. This innovation allows plasma-cut edges to approach the accuracy typically associated with laser cutting. Some manufacturing firms have integrated precise CNC control systems with these new nozzles, resulting in cuts that require minimal further processing or finishing.
Cost-effectiveness compared to alternative cutting methods:
The cost of plasma cutting has significantly decreased over time. In the past, plasma torches were prohibitively expensive, limiting their presence to specialized welding shops and well-equipped private facilities. However, contemporary plasma torches are becoming more accessible and are now within the financial reach of most hobbyists. Traditional equipment often had considerable bulk, even in portable models, whereas modern inverter-equipped types are lightweight yet offer equal or superior performance to older models.
CGSteel offers customized plasma cutting services tailored to your specific material and size requirements. Our capabilities include:
Carbon Steel:
- ASTM A36
- ST37
- ASTM A516
- ASTM A572
- and more Cutting thickness can reach up to 40mm, with tolerances of +/- 1.0 mm.
Stainless Steel:
- 304, 304L
- 316, 316L
- 321
- 310S
- 317
- and more Cutting thickness can reach up to 30mm, with tolerances of +/- 1.0 mm.
Alloy Steel:
- Chrome alloy
- Nickel alloy
Weathering Steel Plate (Corten Steel)
For any plasma cutting requirements, feel free to reach out to us. We're here to assist you.