Flame cutting, also referred to as oxy-fuel cutting, utilizes the intense heat generated by oxy-fuel gas to precisely cut steel materials or hard metals into the required panels or profiles. This method is capable of cutting steel thicknesses ranging from 1 mm to 1200 mm. Typically, it is employed for steel plate thicknesses exceeding 20 mm due to the inherent tolerance associated with oxy-fuel cutting. For steel thicknesses under 20 mm, alternative cutting methods such as laser cutting or waterjet cutting are preferred to achieve higher precision.
However, advancements in oxy-fuel cutting technology have led to the development of high-precision flame cutting, characterized by a precise oxy-fuel gas mixture and meticulous temperature control. This quality flame cutting, particularly when integrated with CNC (Computer Numerical Control) flame cutting technology, has found widespread application in the manufacturing processes of steel parts.
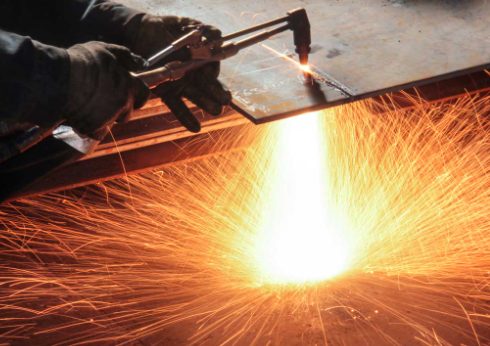
Flame cutting, also known as oxy-fuel cutting or oxyacetylene cutting, involves using a cutting torch that burns oxy-fuel gas to produce a flame. This flame is then used to heat and cut through steels. It's one of the oldest methods used in hot steel cutting. The cutting torch is specifically designed to supply oxygen fuel gas, which burns the iron oxide, ensuring a stable temperature and achieving better cutting performance.
Flame-cut steel is widely used in cutting steels due to its long-standing history and commonality in steel cutting technology. In metal fabrication processes, which involve cutting, heating, and welding steel, various techniques are employed to shape steel. Flame cutting is one such technique, and with advancements in hardware, it's possible to achieve high-quality flame-cut steel parts. This method utilizes fuel gas and oxygen to cut shapes from steel plates, and it has become increasingly popular for a variety of reasons.
Advantages:
- Cost-effectiveness: Flame cutting machines are more economical compared to laser or waterjet machines. Even an oxy-fuel cutting revolver offers cost-effective cutting solutions.
- Suitability for Thick Steel: Flame cutting is the preferred method for cutting thick steel, offering an effective solution where other methods may not be feasible.
- Affordability: This method is relatively affordable when compared to alternative cutting techniques.
- Ability to Cut Large Surfaces: Flame cutting can efficiently cut through large metal surfaces, accommodating thicknesses ranging from 1 millimeter to 1000 millimeters.
- Portability: Flame cutting equipment is portable, enabling its use in various locations beyond a traditional workshop setting.
- Integration with CNC Technology: Flame cutting technology can be integrated with CNC systems, enhancing precision and automation capabilities.
Disadvantages:
- Material Transformation: Cutting parts with flame cutting may result in larger transformations due to the heat, leading to more material melting and distortion.
- Skilled Operator Requirement: Operators must possess high skills and extensive experience to achieve better precision and minimize heat-induced transformations during cutting processes.
Ever wondered about the mechanics behind flame cutting steel plates (also known as oxy-fuel cutting)? If so, you've come to the right place. The flame cutting process is fundamentally thermo-chemical, relying on intense heat generated by pure oxygen. This oxygen, often stored in bulk systems or cylinders, is essential for achieving the high temperatures required for efficient cutting. Using impure oxygen can significantly reduce cutting speed and effectiveness. However, it's crucial to handle pure oxygen with care, as it can pose serious safety risks if mishandled or if leaks occur due to damaged hoses or improper connections.
When it comes to materials suitable for flame cutting, the process is most effective when the oxide formed during cutting has a lower melting point than the material itself. This limitation means that flame cutting is primarily suited for steel and similar materials. For instance, materials like aluminum are not compatible with oxy-fuel cutting due to their oxide properties.
Types of Flame Cutting (Oxy-fuel Cutting)
Flame cutting can be classified into torch cutting and CNC flame cutting (machine flame cutting table).
Torch Cutting: Torch cutting, also known as flame torch cutting, involves the use of a torch, also called a fire gun. The torch's structure varies depending on the type of gas used. The most common torch utilizes Oxygen-Acetylene gas, with acetylene pressure ranging from 0.01 to 0.12 Mpa and oxygen pressure from 0.50 to 1.0 Mpa. In this method, two different gases are burned separately within their channels and then mixed in the oxy-fuel cutting torch, allowing for manual flame adjustment. This type of oxygen cutting is primarily used for re-cutting to remove defects from steel billet cutting or steel straightening.
CNC Flame Cutting for Steels: CNC flame cutting is carried out using a CNC cutting machine, which employs CNC technology to control both the flame cutting table and cutting torch. This process is used for cutting steel plates, steel sheets, and other metal materials. CNC flame cutting equipment consists of three main components: CNC control systems, flame cutting systems, and drive systems.
The advantages of CNC flame cutting for steel include its ability to cut large, thick steel plates at a lower cost. However, it shares similar disadvantages with common flame cutting methods, such as significant transformation, lower precision, slow cutting speed requiring extended preheating time, slow perforation, and difficulties with fully automated operations. As a result, its application is primarily limited to carbon steel and thick steel plate cutting. For thin steel plates under 20 mm, laser cutting or plasma cutting techniques are often preferred alternatives.
Improving Flame Cutting Performance:
Enhancing the effectiveness of flame cutting involves optimizing two key elements: nozzle selection and fuel type. These factors play a significant role in determining both the efficiency of the cutting process and associated costs. The choice of nozzle and fuel can impact labor expenses and cutting speed. Additionally, the composition of the oxy-fuel mixture and the type of gas utilized influence the duration required to cut through a given material.
In most instances, oxygen fuel is combined with other gases like propane, methane, acetylene, propylene, or MAPP to attain the necessary ignition temperature. It's essential to maintain the flame cutting steel temperature below the material's melting point. Following this, pure oxygen fuel is introduced into the preheated zone to initiate the cutting process.
The selection of ignition gas depends on factors such as whether the process is automated or manual, the type of material being cut, and the specifics of the job at hand. It's crucial to choose a gas that can generate the required heat within the allocated budget.
Flame Cutting Thickness Range for Steel Plate:
One of the most frequently asked questions regarding flame cutting pertains to the thickness range of steel plates that can be cut using this method. Flame cutting has a rich history dating back to the peak of industrialization, with proven capabilities to cut materials up to 100 inches thick. This process significantly simplifies the task of cutting materials, including steel plates and panels.
For thinner materials, intensive preheating is necessary to enhance cutting speed and process efficiency. This preheating step remains consistent for thicker materials as well. The thickness of the steel being cut is directly influenced by the amount of oxy-fuel delivered during the cutting process. By adjusting the fuel gas and pure oxygen levels, a smooth cut surface can be achieved to meet specific requirements.
Cutting Temperatures: Typically, the preheating phase involves raising the temperature of a material to approximately 1600-1800 degrees Fahrenheit. Subsequently, pure oxygen is introduced into the heated area to facilitate combustion or oxidation. This process ensures the attainment of a superior final cut surface, characterized by a sharp, slag-free lower edge, a crisp top edge, or a flat cut surface.
Achieving High-Precision Flame-Cut Steel Panels: To obtain flame-cut steel panels or parts of exceptional quality and precision, several crucial factors govern the process. Here are key considerations:
- Thoroughly understanding the operational intricacies of the process is essential. If this proves challenging, seeking the expertise of a professional service provider is advisable.
- Choosing an appropriate cutting tip is paramount for realizing desired cuts effectively. Various tips are available, and opting for a straightforward technique simplifies the attainment of desired outcomes.
- Determining the correct oxy-fuel cutting pressure is crucial, as it aligns with individual requirements and ensures the achievement of desired quality cuts.
- Prioritizing the preheating process is imperative. Neglecting this phase can significantly impact the success of the entire flame cutting process.
- Employing the appropriate cutting speed is essential for meeting predetermined objectives within the allocated timeframe.
Undoubtedly, flame cutting offers a cost-effective means of shaping various materials. However, it's important to note that not everyone achieves high-quality or precise flame-cutting results. Nonetheless, adhering to the aforementioned guidelines minimizes the risk of unsuccessful cuts and enhances the likelihood of achieving desired outcomes.