When purchasing steel pipes for pipeline systems, epoxy coating, such as 3PE (3LPE) or FBE, is commonly requested. Here's a brief overview:
- FBE (Fusion Bonded Epoxy) pipe is coated internally and externally with epoxy coatings. It's primarily used for internal coating of pipes.
- 3LPE (3-Layer Polyethylene) pipe is coated internally with epoxy, has an adhesive layer in the middle, and is coated externally with a polyethylene layer. It's exclusively used for external coating of pipes.
As for costs, the price of the 3PE and FBE coating layers varies depending on factors such as pipe diameter, length, and the specific requirements of the coating process.
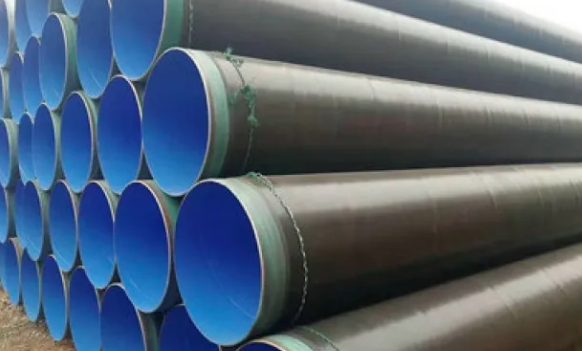
Application of 3LPE/FBE Coated Pipes: 3PE/3LPE coated pipes and FBE epoxy-coated steel pipes find extensive application in pipeline systems for the transportation of oil, gas, water, and various other fluids. These coatings offer exceptional resistance to corrosion caused by chemicals, moisture, and harsh environmental conditions.
Various types of steel pipes are suitable for coating with 3LPE/3PE or FBE, including:
- Stainless steel pipes:
- ASTM A312
- ASTM A269
- Carbon steel pipes:
- API 5L line pipes from Grade B to Grade 80
- ASTM A53 (Hot dipped galvanized steel pipes)
- ASTM A106
- ASTM A252
- ASTM A134 and A135
- ASTM A333
- Alloy steel pipes:
- ASTM A335
- Nickel Alloy pipes
- CRA (Corrosion Resistant Alloy) clad or lined pipes
What is FBE (Fusion Bonded Epoxy) coating steel pipe?
FBE coating pipe is Fusion Bonded Epoxy coating steel pipe. It could be applied for external or internal coating, with heat resin for pipe. With coated a form of dry powder at thickness 400-600 microns on to the heated surface of pipe. Once the FBE coated on the pipe surface, the FBE film provides an extremely hard surface with great adhesion to the pipe surface. The FBE layer in a even form and have good resistance to the chemical reaction.
Features of FBE Epoxy Coated Pipes:
The FBE coating on pipes offers several advantages. It's easy to apply, environmentally friendly with no pollution, and exhibits excellent resistance to high temperatures ranging from -40°C to 85°C. These pipes boast high strength and are resistant to bending, with strong adhesion, ensuring integrity and resistance against soil stress and wear. Typically, FBE coated steel pipes are buried underground or submerged in water, enduring temperatures between -40°C and 85°C.
However, FBE pipes do have drawbacks, notably their limited resistance to mechanical stress and humid conditions.
Types of FBE Epoxy Coated Pipes:
The development of FBE coated pipes dates back to the 1950s, with industrialization occurring in the 1960s. There are two main types: single-layer and dual-layer pipes. Dual-layer FBE coated pipes are recommended for offshore and challenging environments, offering superior impact resistance and flexibility. They also provide protection during transportation and construction.
On the other hand, single-layer FBE coated pipes are the standard variety. They feature a textured surface suitable for concrete coating. These pipes are coated with a special fusion-bonded epoxy powder mixed with solid epoxy resin and other adhesives to ensure proper adhesion to the pipe surface.
Introduction to 3LPE Coated Pipes:
3LPE coated pipes consist of three layers: a fusion-bonded epoxy (FBE) coating, an adhesive layer, and an outer polyethylene layer. This technology emerged in the 1980s as an evolution of FBE coating, offering enhanced mechanical properties, high electrical resistance, waterproofing, wear resistance, and anti-aging properties. Importantly, it significantly reduces heat loss, accounting for only a quarter of the heat loss compared to uncoated pipes.
The three layers of 3LPE coating include:
- Fusion bonded epoxy with a thickness greater than 100μm.
- An adhesive layer, binding the epoxy and PE layers, with a thickness ranging from 170 to 250μm.
- A polyethylene layer providing resistance to water, electrical properties, and protection against mechanical damage, with a diameter ranging from φ300 to φ1020mm.
As a result of combining the benefits of FBE and PE, 3LPE coated pipes are increasingly utilized in buried pipelines for transporting water, gas, and oil.
Moreover, manufacturers of 3PE coating steel pipes can also produce FBE coated pipes, offering versatility in manufacturing equipment.
Benefits and Features of 3PE/3LPE Coated Pipes:
- Corrosion Resistance: 3LPE coated pipes are primarily used for external coating to resist corrosion from the environment, while FBE serves as internal coating to combat fluid corrosion, making them ideal for industries such as chemicals and potable water transmission.
- Durable Lifespan: These pipes exhibit excellent stability and anti-aging properties under normal operating conditions, extending their lifespan to over 50 years.
- Corrosion Protection: The high structural stability of PE elements renders the pipes resistant to corrosion from natural gas, liquefied petroleum gas, and various chemicals, eliminating the need for secondary anti-corrosion measures. Additionally, soil chemicals have no adverse effects on the pipes.
- Flexibility: With its soft and flexible nature, 3PE/3LPE coatings allow pipes to elongate up to 5 times their length before breaking. This flexibility enables easy bending and maneuvering around obstacles, reducing installation costs.
- Impact and Earthquake Resistance: Polyethylene's non-fragile nature at low temperatures (-60℃ to 60℃) ensures safe operation even in harsh conditions, while its excellent impact resistance minimizes the risk of pipe damage.
- Superior Wear Resistance: PE-coated pipes exhibit four times greater wear resistance compared to uncoated pipes, particularly in applications involving mud transport, resulting in reduced maintenance needs.
- Smooth Surface: The smooth internal surface of 3PE/3LPE coated pipes, with a Manning coefficient of 0.009, facilitates efficient fluid transport, reduces pressure loss, and minimizes water permeation, enhancing resistance to seawater compared to other coatings.
- Environmentally Friendly: Manufactured without heavy metal stabilizers and containing no harmful substances, PE materials are environmentally friendly and recyclable, contributing to pollution prevention.
- Excellent Electrical and Anti-static Properties: PE pipelines are suitable for use in flammable and explosive environments due to their outstanding electrical resistance and anti-static characteristics.
- Secure Connection: Utilizing hot melt and fused connections, 3LPE/3PE coated pipes ensure leak-proof joints, enhancing overall pipeline integrity and safety.
- Lightweight and Convenient: With the 3LPE layers weighing only 1/8th of the steel pipe, these pipes are easy to transport, bend, and weld, resulting in faster and more cost-effective construction projects.
Given the significant extension of the lifespan of steel pipes achieved through 3LPE and FBE coatings, their demand has surged in recent pipeline projects. The substantial global economic losses due to steel pipe corrosion underscore the importance of investing in corrosion-resistant coatings. CGSteel offers 3LPE and FBE coated pipes in various standards and types, and we invite you to contact us for tailored solutions to meet your requirements.