Fire protection pipes and fittings serve the crucial role of connecting firefighting equipment and conveying water for fire suppression. Commonly known as fire sprinkler pipes and fittings, they are subject to unique requirements regarding thickness and material due to their specialized function. As per regulations, fire pipelines must be visibly distinguished by being coated with red paint, setting them apart from other pipelines. Given that fire protection pipes often remain static, they are subject to more stringent requirements. These pipes and fittings must demonstrate resilience to pressure, corrosion, and high temperatures.
Based on material, fire protection pipes can be categorized into ductile iron, copper, stainless steel, alloy, composite, and plastic pipes.
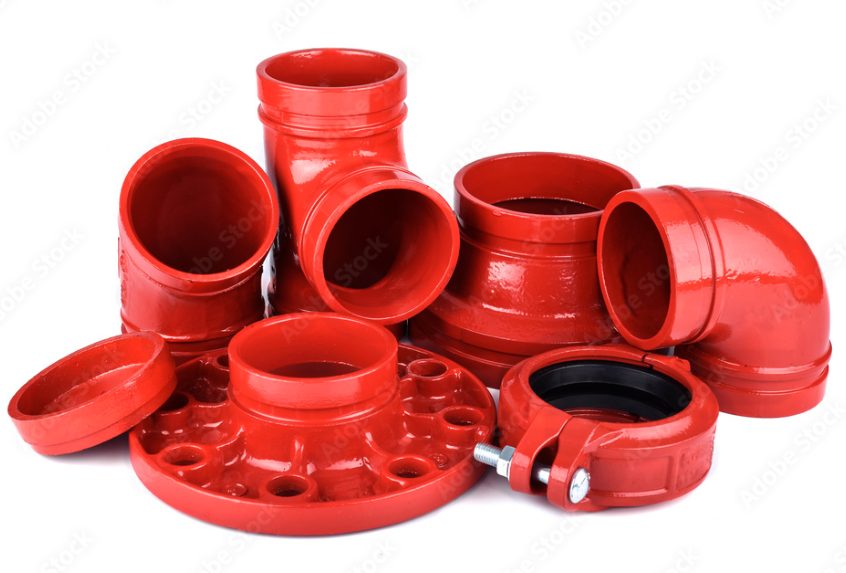
Here's an alternative way to express the installation process flow for a fire pipeline system:
- Preparation for Installation
- Installation of Dry Pipes
- Installation of Alarm Valves
- Vertical Pipe Installation
- Installation of Layered Sprinkler System, Hydrants, and Branch Pipes
- Installation of Water Flow Indicators, Firewater Pumps, High Water Tanks, and Pump Couplings
- Pressure Testing of Pipelines
- Pipeline Flushing
- Installation of Spray Head Branch Pipes (including comprehensive system pressure testing and flushing)
- Installation of Throttle Devices
- Installation of Alarm Valve Accessories, Hydrant Accessories, and Spray Heads
- System Water Testing
Fire protection pipe and fittings employ various connection methods:
- General connection fittings:
- Hot-dip galvanized steel pipes in fire hydrant water supply systems shouldn't be welded. However, if the internal wall of the fire protection pipe lacks anti-corrosive treatment, welding for connection is permissible, adhering to relevant requirements.
- Automatic sprinkler system pipes should not be welded; instead, threaded, flange, or alternative connections are recommended.
- Pipes with a diameter exceeding 100 mm in hydrant water supply systems should use flange or groove connections.
- In automatic sprinkler systems, if the diameter isn't clearly indicated and exceeds 100 mm, threaded connections are prohibited, requiring flange or groove connections at specified intervals.
- When using flange connections in fire hydrant water supply and automatic sprinkler systems, threaded flanges are preferred. Welding flanges necessitate secondary zinc plating.
- Changing pipe diameter in fireproof sections requires compliant connection pipe fittings.
- Groove (clamp) connection:
- Groove depth and pipe joint must meet prescribed standards. Maximum working pressures vary based on nominal diameters.
- Flexible joints are suitable for vibration-prone and buried pipes, while rigid joints are preferable elsewhere, with a flexible joint every 4-5 rigid joints.
- Threaded connection:
- Pipes with inner and outer diameters below 100 mm can use threaded connections.
- Hot-dip galvanized ERW steel pipes can employ malleable iron threaded pipe fittings; hot-dip galvanized seamless steel pipes can utilize forged steel thread pipe fittings.
- Threaded connections are unsuitable for pipes with thin walls below specified thicknesses.
- Sealing methods differ based on thread type.
- Welded or flange joint connection fittings:
- Flanges include flat welding, welded, and threaded types, following relevant standards.
- Hot-dip galvanized steel pipes should use threaded flanges for flange connections, and welding connections may be used for fireproof pipes lacking internal anti-corrosive treatment.