ASTM A516 serves as the standardized guideline for crafting pressure vessels like oil tanks. Specifically tailored for moderate and lower temperature conditions, this specification mandates the use of carbon steel. Its application enhances the steel's notch toughness, particularly crucial during welding operations.
ASTM A516 Grade 70 - Common Use Grade
It is categorized into four grades based on varying strength levels: 55, 60, 65, and 70, with Grade 70 being the most commonly utilized.
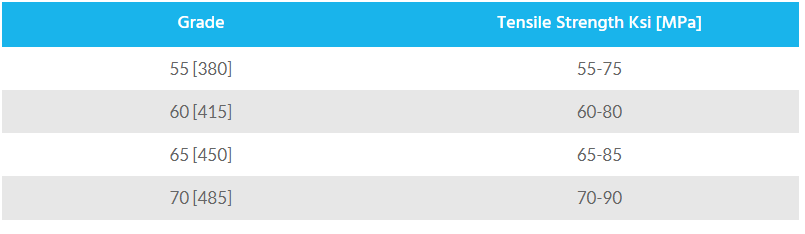
Plate Thickness Constraints:
The maximum allowable thickness of plates is determined solely by the capacity of the material composition to satisfy the specified mechanical property standards. Plates manufactured from coils and provided without heat treatment or solely stress-relieved must adhere to the requirements and test outcomes outlined in A20/A20M. Coils are not qualified under this specification until they are cut into plates.
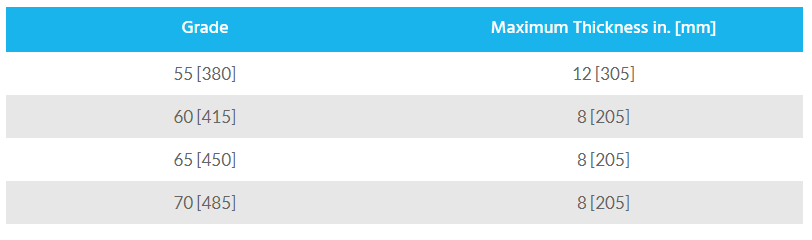
Documents Cited for Reference: ASTM Standards:
- A20/A20M: General prerequisites for steel plates used in pressure vessels and tanks
- A435/A435M: Guidelines for straight-beam ultrasonic inspection of steel plates
- A577/A577M: Procedures for angle-beam ultrasonic inspection of steel plates
- A578/A578M: Standards for straight-beam ultrasonic examination of rolled plates intended for specialized applications
Specifications and Production Details for A516 Plates
The steel used must be fully deoxidized and meet the fine austenitic grain size requirement outlined in SPEC A20/A20M.
Heat Treatment Plates with a thickness of 40 mm [1.5 in] or less are typically supplied in their as-rolled state. However, if normalization or stress relief is necessary, this must be communicated prior to placing the order.
Plates exceeding 40 mm [1.5 in] in thickness are to be normalized.
For plates with a thickness of 1.5 in [40 mm] or less requiring notch-toughness tests, normalization is the default unless otherwise specified by the purchaser.
Upon agreement with the purchaser, accelerated cooling rates beyond air cooling are acceptable to enhance toughness, provided that subsequent tempering is performed within the range of 1100 to 1300℉ [595 to 705 ℃].