Boilers play a crucial role in various industries, from power generation to manufacturing processes. Central to their efficiency and reliability are the materials used in their construction, particularly in boiler pipes. The choice of metal for these pipes is vital, as it directly impacts performance, longevity, and safety. So, which metal is commonly used in boiler pipes, and why? Let's delve into the intricacies.
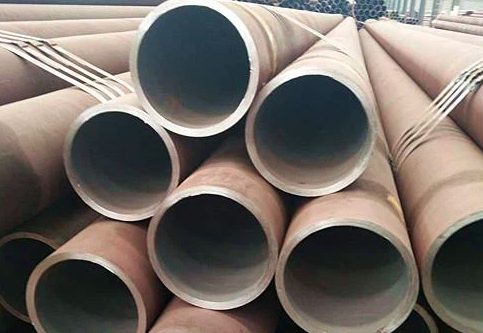
Stainless Steel: A Top Contender
Among the various metals utilized in boiler pipes, stainless steel stands out as a preferred choice for many applications. Its inherent properties make it well-suited for the demanding conditions within boilers. Stainless steel offers excellent resistance to corrosion, high temperatures, and pressure, all of which are prevalent in boiler environments.
Corrosion is a significant concern in boilers due to the presence of water and steam. Stainless steel's corrosion resistance, especially against acidic and alkaline environments, helps maintain the integrity of boiler pipes over extended periods. Additionally, its ability to withstand high temperatures without significant deformation or degradation ensures optimal performance under challenging operating conditions.
Furthermore, stainless steel offers superior strength-to-weight ratio compared to many other metals, allowing for the construction of durable and lightweight boiler systems. This characteristic is particularly advantageous in large-scale industrial applications where efficiency and reliability are paramount.
Carbon Steel: Widely Used for its Durability
Carbon steel is another prevalent choice for boiler pipes, owing to its durability, cost-effectiveness, and ease of fabrication. Carbon steel exhibits robust mechanical properties, making it suitable for handling high-pressure and high-temperature conditions commonly encountered in boiler operations.
While carbon steel lacks the corrosion resistance of stainless steel, proper surface treatments and coatings can mitigate corrosion issues effectively. Additionally, advancements in material science have led to the development of corrosion-resistant variants of carbon steel, further enhancing its suitability for boiler applications.
Carbon steel's widespread availability and relatively lower cost compared to stainless steel make it an attractive option for budget-conscious projects without compromising on performance and reliability. However, proper maintenance and monitoring are essential to prevent corrosion and ensure the longevity of carbon steel boiler pipes.
Alloy Steel: Balancing Strength and Corrosion Resistance
Alloy steel represents a category of metals that combine various elements to achieve specific mechanical properties tailored to the demands of boiler applications. Alloying elements such as chromium, molybdenum, and nickel are commonly added to enhance corrosion resistance, strength, and toughness.
Alloy steel offers a balanced combination of strength and corrosion resistance, making it suitable for a wide range of boiler configurations and operating conditions. By adjusting the composition and heat treatment, engineers can tailor alloy steel properties to meet the precise requirements of boiler systems, optimizing performance and durability.
The choice of metal in boiler pipes is a critical decision that impacts the efficiency, reliability, and safety of boiler operations. While stainless steel, carbon steel, and alloy steel are among the primary options, each has its unique advantages and considerations.
Stainless steel shines in corrosive environments, offering excellent resistance to degradation over time. Carbon steel, on the other hand, provides durability and cost-effectiveness, albeit with a need for proactive corrosion prevention measures. Alloy steel strikes a balance between strength and corrosion resistance, offering versatility in various boiler applications.
Ultimately, the selection of metal for boiler pipes should be guided by a thorough assessment of the specific operating conditions, budget constraints, and performance requirements. By leveraging the strengths of different metals and employing appropriate engineering practices, boiler systems can achieve optimal performance and longevity, ensuring uninterrupted operations across diverse industries.