In the realm of metallurgy, the development of alloy pipes has revolutionized various industries, ranging from construction to manufacturing. These specialized pipes offer a unique blend of properties that make them indispensable in applications where strength, durability, and corrosion resistance are paramount. Let's delve into what precisely defines an alloy pipe and why it has become a cornerstone in modern engineering.
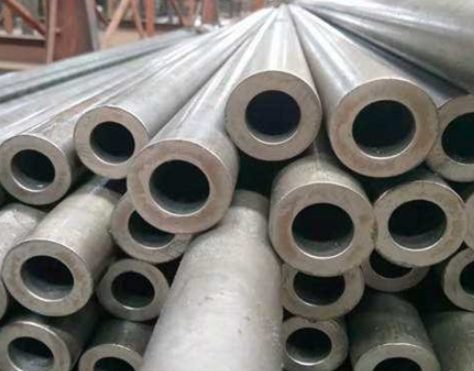
Understanding Alloy Pipes: Alloy pipes are fabricated from a combination of two or more metallic elements, often including iron as a base metal. Unlike conventional steel pipes, which primarily consist of iron and carbon, alloy pipes incorporate additional elements such as chromium, nickel, copper, or molybdenum. These additives alter the material's properties, enhancing its performance in specific environments or applications.
The amalgamation of different elements imparts distinctive characteristics to alloy pipes, making them highly adaptable to diverse conditions. For instance, chromium-enriched alloys exhibit exceptional corrosion resistance, making them ideal for applications exposed to corrosive fluids or harsh environments. Meanwhile, nickel-based alloys excel in high-temperature settings, offering superior strength and stability even at elevated temperatures.
Applications of Alloy Pipes: The versatility of alloy pipes finds extensive applications across various industries:
- Oil and Gas: Alloy pipes play a pivotal role in the extraction, transportation, and refining of oil and natural gas. Their corrosion resistance and high-pressure capabilities make them indispensable for pipelines operating in corrosive environments or under extreme pressures.
- Chemical Processing: In chemical plants, where exposure to corrosive chemicals is commonplace, alloy pipes provide a reliable solution. Their resistance to chemical corrosion ensures the integrity of the piping systems, safeguarding both personnel and the environment.
- Power Generation: Alloy pipes are integral components in power generation facilities, particularly in boilers and heat exchangers. Their ability to withstand high temperatures and pressures ensures the efficiency and safety of power generation processes.
- Aerospace and Automotive: In aerospace and automotive applications, where weight reduction and durability are critical, alloy pipes find usage in engine components, exhaust systems, and structural frameworks.
Benefits of Alloy Pipes: The adoption of alloy pipes offers several advantages over conventional piping materials:
- Enhanced Strength: Alloy pipes exhibit superior strength and toughness, allowing them to withstand high pressures and mechanical stresses without deformation or failure.
- Corrosion Resistance: The incorporation of corrosion-resistant elements mitigates the risk of rust and degradation, prolonging the lifespan of piping systems and reducing maintenance requirements.
- Temperature Stability: Certain alloy compositions maintain their mechanical properties even at extreme temperatures, ensuring reliability in both high-temperature and cryogenic applications.
- Customizability: Alloy compositions can be tailored to meet specific performance requirements, allowing for the customization of pipes based on application needs.
Alloy pipes represent a remarkable fusion of science and engineering, offering a versatile solution to the challenges posed by demanding industrial environments. Their unique blend of properties, including strength, corrosion resistance, and temperature stability, has propelled them to the forefront of modern engineering. As industries continue to evolve and demand higher performance standards, alloy pipes will undoubtedly remain indispensable components in the infrastructure that drives global progress.