In the world of metallurgy, the diversity of steel alloys can be quite bewildering. Among the myriad types, silicon steel and carbon steel stand out prominently, each with its unique properties and applications. Understanding the disparities between these two materials is crucial for anyone delving into the realms of manufacturing, engineering, or simply seeking knowledge about the materials shaping our modern world.
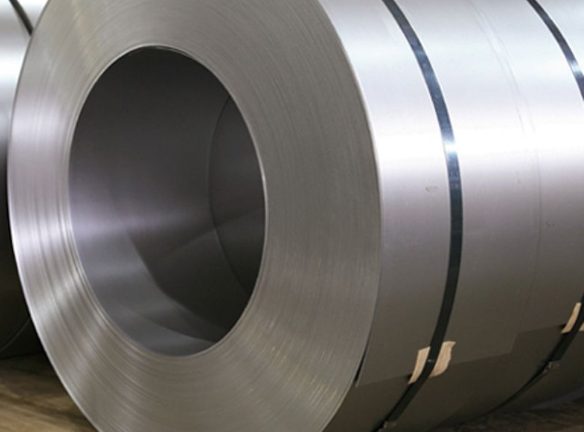
Silicon Steel: The Transformer's Ally
Silicon steel, also known as electrical steel or transformer steel, finds its niche in electrical applications due to its magnetic properties. This specialized steel variant contains varying amounts of silicon, typically between 1% and 3.5%, alongside small amounts of other elements such as carbon and manganese.
Key Characteristics:
- High Magnetic Permeability: Silicon steel exhibits high magnetic permeability, making it an ideal choice for transformers, electric motors, and other electromagnetic devices.
- Low Core Loss: The presence of silicon reduces eddy current losses, enhancing the efficiency of electrical equipment by minimizing energy dissipation in the form of heat.
- Grain-Oriented vs. Non-Grain-Oriented: Silicon steel comes in two main types: grain-oriented and non-grain-oriented. Grain-oriented silicon steel possesses a directional grain structure, optimizing its magnetic properties in specific orientations, whereas non-grain-oriented silicon steel offers isotropic properties suitable for diverse applications.
- Thin Gauge Sheets: It is often produced in thin gauge sheets to minimize energy losses in electrical transformers and generators.
Carbon Steel: The Workhorse of Industry
Carbon steel, on the other hand, is the quintessential workhorse of the metallurgical world. It is a broad category encompassing various steel alloys where the primary alloying element is carbon, typically in concentrations ranging from 0.05% to 2.1%.
Key Characteristics:
- Versatility: Carbon steel is highly versatile, with a wide range of applications spanning construction, automotive, infrastructure, and machinery sectors.
- Strength and Hardness: Depending on carbon content and heat treatment, carbon steel can exhibit varying degrees of strength and hardness, making it suitable for load-bearing structures and tools.
- Ease of Forming and Welding: Carbon steel is relatively easy to form and weld, facilitating its use in manufacturing processes where shaping and joining are essential.
- Cost-Effectiveness: Compared to many other alloys, carbon steel tends to be more cost-effective, making it a preferred choice for large-scale industrial applications.
Contrasting Attributes
While both silicon steel and carbon steel are integral to diverse industrial sectors, their disparities are notable:
- Composition: Silicon steel contains significant amounts of silicon alongside iron, while carbon steel primarily consists of iron and carbon.
- Properties: Silicon steel boasts magnetic properties suitable for electrical applications, whereas carbon steel exhibits mechanical properties like strength and hardness.
- Applications: Silicon steel finds its main use in electrical transformers, motors, and generators, while carbon steel is ubiquitous in construction, manufacturing, and infrastructure projects.
In essence, while both silicon steel and carbon steel share the commonality of being steel alloys, their unique compositions and properties tailor them for distinct roles in the industrial landscape.
Understanding the disparities between silicon steel and carbon steel is paramount for engineers, manufacturers, and enthusiasts alike. Whether it's harnessing the magnetic prowess of silicon steel in electrical transformers or relying on the robustness of carbon steel in construction projects, appreciating the distinct attributes of these materials is essential for informed decision-making in various industries. So, the next time you encounter these steel variants, remember, it's not just steel; it's a world of difference.