In the realm of metallurgy, silicon steel has long been hailed as a cornerstone material, particularly in electrical engineering and transformer manufacturing. Renowned for its magnetic properties and unparalleled efficiency in electrical applications, silicon steel has undeniably revolutionized numerous industries. However, amidst its myriad advantages, lies a set of disadvantages that warrant consideration. Delving deeper into the intricacies of this material reveals its limitations, which are crucial for engineers, manufacturers, and consumers alike to acknowledge.
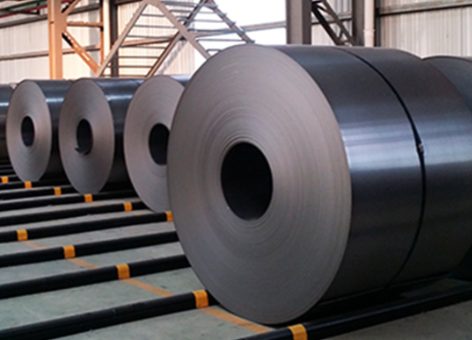
- Brittleness: One of the primary drawbacks of silicon steel is its inherent brittleness. While it boasts exceptional magnetic properties, this brittleness can pose challenges during manufacturing processes, especially when shaping or stamping the material into desired forms. This brittleness can increase the likelihood of cracks or fractures, leading to potential structural weaknesses in the final product.
- Susceptibility to Corrosion: Despite efforts to mitigate corrosion through various coating techniques, silicon steel remains vulnerable to rust and corrosion over time. Exposure to moisture or harsh environmental conditions can accelerate this process, compromising the integrity and longevity of components made from silicon steel. This susceptibility necessitates rigorous maintenance and protective measures, adding to the overall cost and complexity of utilizing silicon steel in applications.
- Limited High-Temperature Stability: Silicon steel exhibits diminished magnetic properties at elevated temperatures, which can significantly impact its performance in applications where thermal stability is paramount. In scenarios involving high temperatures, such as in motors or generators, the magnetic characteristics of silicon steel may degrade, leading to reduced efficiency and reliability. Alternative materials with superior heat resistance may be preferred in such demanding environments.
- High Cost: While silicon steel offers unparalleled magnetic properties, its production process involves complex alloying techniques and precise manufacturing methods, resulting in relatively high production costs. Additionally, the fluctuating prices of raw materials, such as silicon and iron, can further contribute to the overall cost of silicon steel. These elevated costs may deter some manufacturers from adopting silicon steel in favor of more economical alternatives.
- Limited Availability of High-Quality Silicon: The quality of silicon used in the production of silicon steel significantly impacts its magnetic properties and overall performance. Obtaining high-purity silicon suitable for alloying can be challenging and expensive, particularly as demand for silicon steel continues to rise. This limited availability of high-quality silicon poses a potential constraint on the scalability and widespread adoption of silicon steel in various industries.
Silicon steel undoubtedly offers remarkable magnetic properties and has revolutionized numerous technological applications, it is essential to acknowledge its inherent limitations. From brittleness and susceptibility to corrosion to high production costs and limited high-temperature stability, these disadvantages underscore the importance of careful consideration when selecting materials for specific engineering and manufacturing endeavors. By recognizing and addressing these drawbacks, researchers and engineers can continue to innovate and enhance the performance and reliability of silicon steel, ensuring its continued relevance in the ever-evolving landscape of materials science and engineering.