When it comes to selecting the right materials for construction and manufacturing, the choice between PPGI (Pre-Painted Galvanized Iron) and PPGL (Pre-Painted Galvalume) becomes pivotal. These two coated steel products share similarities, yet their differences play a crucial role in determining their suitability for specific applications. In this article, we'll delve into the characteristics that distinguish PPGI from PPGL, shedding light on their unique features and applications.
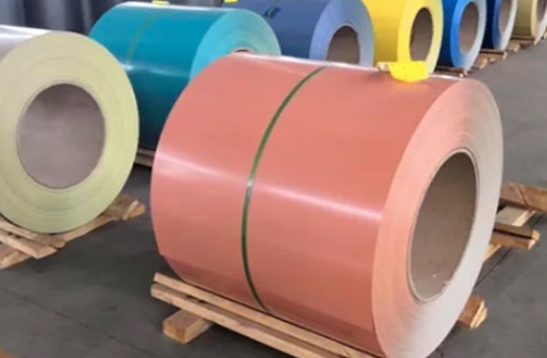
PPGI: Pre-Painted Galvanized Iron
PPGI, or Pre-Painted Galvanized Iron, is a popular coated steel product that starts with a base of galvanized steel. The galvanization process involves applying a layer of zinc to the steel surface, providing it with corrosion resistance. Subsequently, the steel is coated with a layer of primer before receiving its final layer of paint.
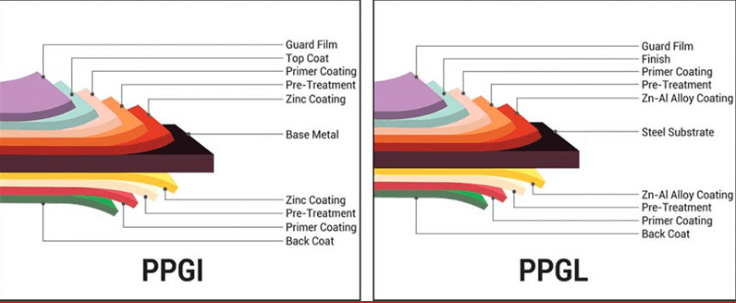
Key Features of PPGI:
- Zinc Coating: The initial layer of zinc offers excellent corrosion protection, making PPGI a preferred choice for environments prone to harsh weather conditions.
- Color Variety: PPGI comes in a wide array of colors, allowing for customization to meet specific aesthetic requirements.
- Applications: PPGI is commonly used in roofing, walling, and other construction applications where durability and corrosion resistance are paramount.
PPGL: Pre-Painted Galvalume
PPGL, or Pre-Painted Galvalume, shares similarities with PPGI but distinguishes itself in terms of the base material. Galvalume consists of a zinc-aluminum alloy, providing enhanced corrosion resistance compared to traditional galvanized steel.
Key Features of PPGL:
- Zinc-Aluminum Alloy: The galvalume base of PPGL combines zinc and aluminum, offering superior corrosion resistance and increased longevity compared to PPGI.
- Heat Resistance: PPGL performs well under high-temperature conditions, making it suitable for applications where heat resistance is crucial.
- Applications: PPGL is often chosen for roofing, cladding, and other outdoor applications where prolonged exposure to challenging weather conditions is expected.
Distinguishing Factors:
- Corrosion Resistance: While both PPGI and PPGL offer corrosion resistance, PPGL, with its zinc-aluminum alloy base, generally provides a higher level of protection against rust and deterioration.
- Cost: PPGI is often more cost-effective than PPGL due to the difference in the base materials. The choice between the two may depend on the budget constraints of a particular project.
- Environment: The selection between PPGI and PPGL may be influenced by the environmental conditions of the intended application. For coastal or highly corrosive environments, PPGL might be the preferred choice.
The choice between PPGI and PPGL depends on specific project requirements and environmental factors. While both offer pre-painted convenience and a range of color options, the underlying distinctions in base materials make each product suitable for different applications. Whether it's the robust zinc-coated PPGI or the corrosion-resistant zinc-aluminum alloy of PPGL, understanding these differences empowers decision-makers to choose the right coated steel product for their construction and manufacturing needs.