Hot rolled steel is a widely used material in various industries, renowned for its cost-effectiveness and malleability. While it boasts several advantages, it's essential to acknowledge the disadvantages that come with its manufacturing process. In this article, we will delve into the drawbacks of hot rolled steel and explore how these limitations might impact its suitability for certain applications.
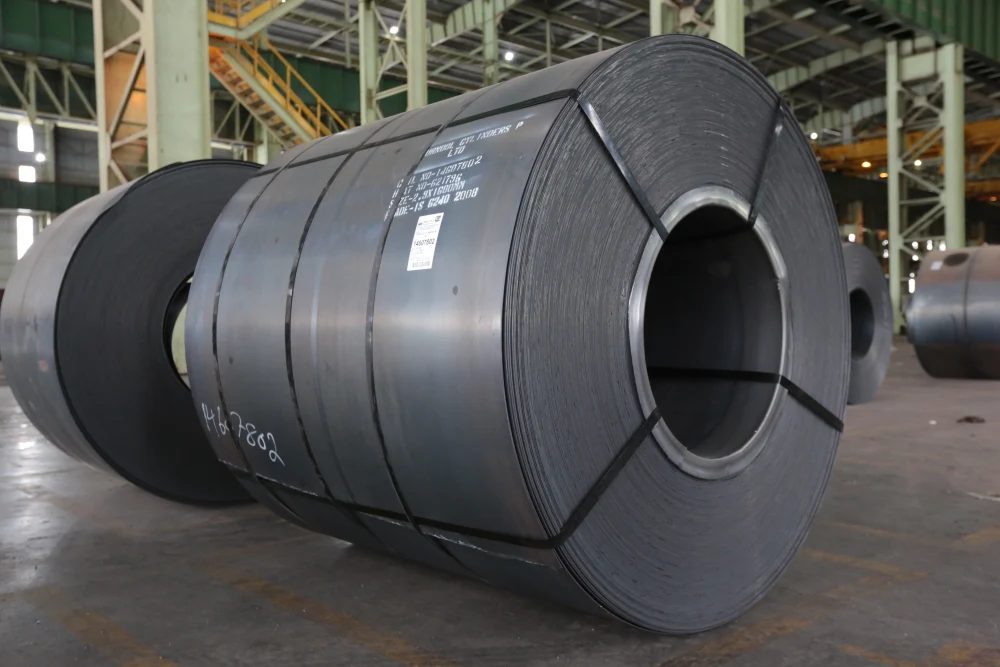
- Surface Finish: One of the primary disadvantages of hot rolled steel is its surface finish. The process involves heating the steel above its recrystallization temperature, followed by rolling it into shape. This can result in a less smooth and uniform surface compared to cold rolled steel. The rougher surface may be undesirable for applications where aesthetics and a polished finish are crucial.
- Dimensional Inaccuracy: Hot rolling can lead to dimensional variations in the final product. The cooling process after hot rolling may not be uniform, causing inconsistencies in thickness and dimensions. This lack of precision might be a significant drawback in applications that require tight tolerances and exact specifications.
- Residual Stress: Hot rolled steel often retains residual stress from the intense heat and cooling process. This stress can lead to distortion or warping of the material, especially in larger or more complex shapes. It becomes crucial to consider this factor in applications where dimensional stability is critical.
- Grain Structure and Mechanical Properties: The hot rolling process can affect the grain structure of the steel, leading to changes in its mechanical properties. While hot rolled steel generally exhibits good strength, it may not be as suitable for applications requiring enhanced surface hardness or precise mechanical characteristics. Cold rolled steel is often preferred in such cases.
- Edge Cracking and Surface Oxidation: During hot rolling, the edges of the steel can be susceptible to cracking. Additionally, the exposure to high temperatures can result in surface oxidation, forming a layer of scale on the steel. These issues can compromise the overall integrity and appearance of the material.
- Limited Shape Complexity: Hot rolling is more suitable for simpler shapes and profiles. It may not be the ideal choice for intricate designs or components requiring high precision. Cold rolled steel is often preferred for applications where intricate shapes and tight tolerances are essential.
While hot rolled steel is a versatile and cost-effective material, it's essential to consider its limitations before choosing it for specific applications. Understanding the drawbacks related to surface finish, dimensional accuracy, residual stress, grain structure, edge cracking, and shape complexity allows for informed decision-making. Engineers and manufacturers must carefully evaluate the requirements of their projects to determine whether hot rolled steel aligns with their desired outcomes or if alternative processes, such as cold rolling, may be more suitable.