Cold-rolled steel has long been a popular choice in various industries due to its smooth finish, tight tolerances, and improved surface quality. However, like any material, it comes with its own set of disadvantages that warrant consideration. In this article, we will delve into the drawbacks of cold-rolled steel, shedding light on aspects that may influence decision-making in material selection.
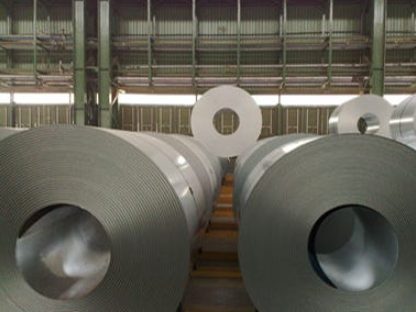
- Increased Cost: One notable disadvantage of cold-rolled steel is its higher production cost compared to hot-rolled steel. The cold-rolling process involves additional steps, such as annealing and tempering, contributing to increased manufacturing expenses. This cost factor may be a crucial consideration for projects with tight budget constraints.
- Limited Shape and Size Options: Cold-rolled steel is often limited in terms of the variety of shapes and sizes available. The cold-rolling process works best with thinner gauges, making it less suitable for applications requiring thicker sections. This limitation might constrain design possibilities, especially in projects where specific dimensions are crucial.
- Work Hardening: Cold-rolled steel is susceptible to work hardening, a phenomenon where the material becomes increasingly difficult to deform. While work hardening can enhance strength, it may lead to challenges during subsequent fabrication processes, such as bending or forming, requiring additional precautions and tooling adjustments.
- Surface Damage and Scratching: The improved surface finish of cold-rolled steel can be a double-edged sword. While it provides a polished appearance, the material is more prone to scratching and surface damage during handling, transportation, or fabrication. This vulnerability may necessitate careful handling throughout the production and installation phases.
- Less Ductility: Cold-rolled steel tends to exhibit reduced ductility compared to its hot-rolled counterpart. This reduced ability to deform without breaking may limit its suitability for certain applications that require a higher degree of flexibility or formability.
- Environmental Considerations: The cold-rolling process often involves the use of lubricants and coolants, contributing to potential environmental concerns. The disposal of these substances must be managed carefully to mitigate environmental impacts, adding an extra layer of responsibility for manufacturers and end-users.
While cold-rolled steel boasts several advantages, including improved surface quality and dimensional accuracy, it is essential to weigh these benefits against the associated disadvantages. The decision to opt for cold-rolled steel should be based on a thorough evaluation of project requirements, budget constraints, and the specific properties needed for the intended application. By understanding the drawbacks, stakeholders can make informed choices and explore alternative materials when necessary.