Stainless steel is a versatile and widely used material in various industries, renowned for its corrosion resistance, durability, and aesthetic appeal. Among the numerous stainless steel grades available, two stand out prominently – 304 and 316. In this article, we will delve into the key distinctions between these two alloys, shedding light on their unique properties and applications.
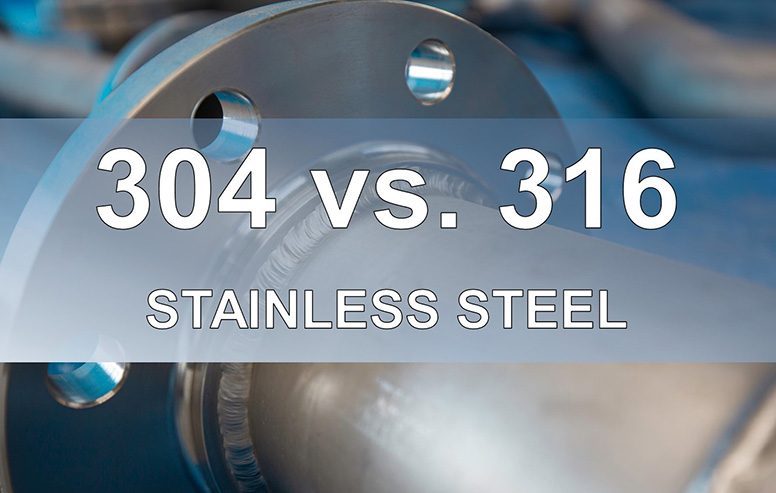
Understanding Stainless Steel:
Before delving into the specifics of 304 and 316 stainless steel, it's crucial to grasp the fundamental characteristics of stainless steel as a whole. Stainless steel is an alloy of iron, chromium, nickel, and other elements, designed to resist corrosion and staining. The addition of chromium forms a protective oxide layer on the surface, which imparts its corrosion-resistant properties.
304 Stainless Steel:
304 stainless steel is one of the most commonly used stainless steel grades. It contains 18% chromium and 8% nickel, making it an austenitic stainless steel. This composition provides excellent corrosion resistance, especially in moderately corrosive environments. Additionally, 304 stainless steel is non-magnetic, making it suitable for various applications, including kitchen appliances, architectural structures, and industrial equipment.
316 Stainless Steel:
316 stainless steel, on the other hand, is an austenitic stainless steel alloy with a slightly different composition. It contains 16% chromium, 10% nickel, and 2% molybdenum. The addition of molybdenum enhances its corrosion resistance, particularly in aggressive and chloride-rich environments. Consequently, 316 stainless steel is often referred to as "marine-grade" stainless steel, making it ideal for applications in coastal and marine environments.
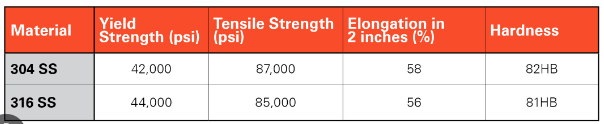
Distinguishing Factors:
- Corrosion Resistance:
- 304: Suited for mild environments and general applications.
- 316: Superior corrosion resistance, especially in harsh and chloride-laden conditions.
- Molybdenum Content:
- 304: Lacks molybdenum.
- 316: Contains 2% molybdenum, enhancing resistance to pitting and crevice corrosion.
- Applications:
- 304: Commonly used in kitchen appliances, architectural structures, and industrial equipment.
- 316: Preferred for marine applications, pharmaceutical equipment, and chemical processing.
- Cost Considerations:
- 304: Generally more affordable than 316 stainless steel.
- 316: Higher cost due to the additional alloying elements.
While both 304 and 316 stainless steel exhibit remarkable corrosion resistance and durability, the key differences lie in their composition and suitability for specific environments. Choosing between them depends on the intended application, environmental factors, and budget considerations. By understanding these disparities, individuals and industries can make informed decisions when selecting the appropriate stainless steel grade for their needs.