Pipeline steel is the backbone of the vast network of energy transportation systems, ensuring the safe and efficient delivery of oil and gas across the globe. The choice of materials for pipeline construction is critical, as it directly impacts the pipeline's durability, performance, and overall safety. In this article, we will explore the materials commonly used for pipeline steel and the factors that make them ideal for this crucial infrastructure.
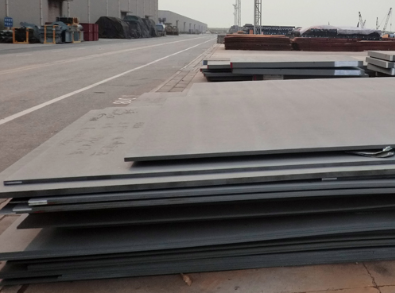
- Carbon Steel: The Workhorse of PipelinesThe majority of pipelines are constructed using carbon steel due to its exceptional mechanical properties and cost-effectiveness. Carbon steel is an alloy of iron and carbon, with small amounts of other elements like manganese, sulfur, phosphorus, and silicon. This composition gives it the strength and durability required for long-distance transportation of oil and gas.
- API 5L Standards: Ensuring Quality and ConsistencyThe American Petroleum Institute (API) has established standards, specifically API 5L, to regulate the manufacturing of steel pipes for the oil and gas industry. These standards define various grades of steel based on their chemical composition and mechanical properties, ensuring consistency and reliability in pipeline construction.
- X52, X60, X70: Grades of Pipeline SteelDifferent grades of pipeline steel are designated based on their yield strength, ranging from X42 to X80 and beyond. For instance, X52 steel has a minimum yield strength of 52,000 psi, making it suitable for pipelines in moderate to high-pressure environments. X60 and X70 are commonly used in more challenging conditions, such as deep-sea pipelines and those traversing harsh terrains.
- Corrosion Resistance: Protecting Against the ElementsPipelines are often exposed to harsh environmental conditions, including moisture, soil chemicals, and corrosive substances. To combat corrosion and ensure the longevity of the pipeline, steel may be coated with protective layers, such as fusion-bonded epoxy or three-layer polyethylene. These coatings act as a barrier, preventing corrosion and maintaining the structural integrity of the pipeline.
- High-Frequency Welding: Enhancing Structural IntegrityThe welding process plays a crucial role in pipeline construction. High-frequency welding (HFW) is a common technique used to join steel pipes seamlessly. This method ensures strong, reliable connections, contributing to the overall structural integrity of the pipeline. The welded joints must undergo rigorous testing, including ultrasonic and radiographic examinations, to identify potential defects and guarantee the pipeline's safety.
In the intricate web of energy transportation, pipeline steel stands tall as the unsung hero, ensuring the seamless flow of oil and gas across vast distances. The careful selection of materials, adherence to industry standards, and the incorporation of advanced welding techniques collectively contribute to the robustness of pipeline infrastructure. As we continue to rely on these essential conduits, understanding the materials used for pipeline steel becomes paramount, highlighting the fusion of science and engineering that propels our energy-driven world forward.