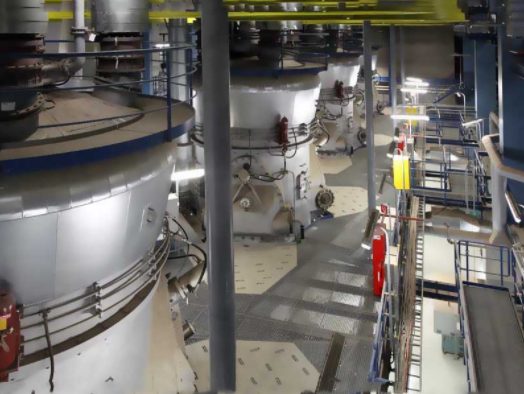
The heat-resistant steel used in manufacturing boiler compression components primarily consists of low-alloy high-strength steel, austenitic stainless steel, and martensitic hot-rolled steel. It is crucial for the steel to exhibit good high-temperature oxidation resistance and enduring strength. The key alloying elements include Cr, Si, and Al, as they facilitate the formation of a complete, dense, and stable oxide protective film on the steel's surface. However, adding Si and Al can render the steel more brittle, so their inclusion is typically balanced with Cr-based elements.
The strengthening mechanism for hot steel differs from that at room temperature. High-temperature deformation is not solely a result of intracrystalline slip; it also involves the contributions of diffusion and grain boundary slip. Diffusion promotes dislocation movement caused by deformation, while grain boundary slip itself can lead to deformation. At high temperatures, grain boundary strength is lower than crystal strength, making grains prone to slipping and causing deformation. Therefore, enhancing the high-temperature strength of steel should focus on three aspects: solid solution strengthening, precipitation strengthening (dispersion strengthening), and grain boundary strengthening.
Low alloy heat resistant steel
- 12CrMoG is a commonly used low-alloy hot steel with 0.5% Cr and 0.5% Mo. The addition of Cr enhances the steel's oxidation resistance and high-temperature strength, while Mo improves its stability and strength at high temperatures. Operating between 480 ℃ and 540 ℃, the steel exhibits sufficient thermal strength and operational reliability, maintaining stability in its structure and high strength over prolonged periods. It does not tend to graphitize, is not prone to hot brittleness, and possesses good processability and weldability, along with high resistance to fatigue.
- 15CrMoG is a widely utilized pearlitic chrome molybdenum heat-resistant steel, offering good process performance, welding capabilities, and high-temperature strength. It is equivalent to the United States T11, T12, and P11, P12, as well as Japan's STBA21, STBA22, STBA23. The steel exhibits no graphitization tendency during long-term operation between 500 ℃ and 550 ℃, but it may undergo pearlitic spheroidization, leading to changes in alloying elements and carbide types, resulting in reduced high-temperature performance.
- 12Cr1MoVG is a low-alloy hot steel with pearlite structure. It contains a small amount of V to enhance stability and thermal strength when alloy transition to carbide occurs during prolonged high-temperature use. The steel is mainly employed for the production of heating surfaces with a wall temperature not exceeding 570 ℃, headers with a wall temperature ≤ 550 ℃, steam pipes, and large forgings.
- 12Cr2MoWVTiB (steel 102) is a low-carbon, low-alloy bainite-type heat-strengthened steel, primarily strengthened by Mo, W composite solid solution, V, Ti composite dispersion, and micro B strengthening. The addition of B strengthens the grain boundaries and facilitates the transformation to a single bainite structure. This steel is mainly used for high-pressure boiler superheaters, reheaters, and other high-temperature components with a wall temperature ≤ 600 ℃.
- 12Cr3MoVSiTiB (п11) is another low-carbon, low-alloy bainite-type heat steel. Compared to 12Cr2MoWVTiB, it possesses higher antioxidant properties but a slightly lower lasting strength. The steel is mainly employed for ultra-high-pressure and subcritical boiler superheaters and reheaters with a wall temperature not exceeding 600 ℃.
Austenitic stainless steel
In high-temperature conditions, austenite exhibits superior stability and strength compared to ferrite, demonstrating excellent thermochemical stability and high-temperature strength, with a maximum oxidation temperature reaching 850 ℃. This steel also boasts outstanding welding and processing performance. However, the alloy elements contribute to a higher cost, as they exceed 26%. Austenitic stainless steels like 1Cr19Ni9 and 0Cr19Ni9 (equivalent to US TP304, TP304H, and Japan's SUS304TB, SUS304TP) possess exceptional processing and welding characteristics, exhibiting good organizational stability and thermal strength with a maximum temperature limit of 650 ℃.
The high oxidation temperature, reaching up to 850 ℃, makes it suitable for the manufacturing of large-scale boiler superheaters, reheaters, and steam pipes. For boiler tubes requiring an oxidation temperature limit of 705 ℃, these steels prove effective. Similarly, 1Cr19Ni11Nb and 0Cr18Ni11Nb (equivalent to TP347, TP347H, SUS347TB, SUS347TP) are Nb-stabilized austenitic hot-rolled steels, known for their high thermal strength, resistance to intergranular corrosion, and excellent processing and welding performance. Primarily used in the production of large-scale boiler superheaters, reheaters, and steam pipes, these steels maintain a maximum operating temperature of 650 ℃, meeting the oxidation temperature limit for boiler tubes at 705 ℃.
Additionally, 0Cr17Ni12Mo2 (equivalent to TP316, TP316H, SUS316TB, SUS316TP) represents a common austenitic stainless steel for heat applications. With 2% to 3% Mo content, this steel exhibits significantly improved corrosion resistance, making it suitable for large-scale boiler superheaters, reheaters, and steam pipes, as well as high-temperature corrosion-resistant bolts and components prone to point corrosion.
Martensitic hot steel
In recent years, 10Cr9Mo1VNb, also known as T91, P91, 1X20CrMoVNb91, STBA28 in China, has gained widespread use. This martensitic steel was initially developed by the United States ORNL (Oak Ridge National Laboratory). Tables 15-1g to 15-1j provide the chemical composition and mechanical properties, respectively. Derived from 9Cr-1Mo (T9, P9) by reducing carbon content and incorporating alloying elements V and Nb, while controlling N and Al content, the steel exhibits excellent oxidation resistance, high-temperature steam corrosion resistance, impact toughness, and stable long-term plasticity and heat strength. Primarily utilized in the manufacturing of subcritical and supercritical boiler components such as high-temperature superheaters, reheaters, high-temperature headers, and steam pipes. Applicable conditions include a wall temperature of ≤625 ℃ for superheaters, ≤650 ℃ for reheaters, and ≤600 ℃ for headers and steam pipes.