Advancement in the Production of Stainless Steel Welded Tubes
In recent times, the progress of stainless steel welded pipes has been notable, witnessing significant advancements in scale, quality, and production technology. Notably, the demand for these pipes has steadily expanded. Furthermore, with the increasing maturity of the stainless steel welded pipe process, it has begun to find broader applications, gradually substituting stainless steel seamless pipes in various areas such as heat exchanger equipment and medium to low-pressure boiler tubes.
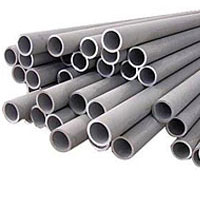
Characteristics of Stainless Steel Welded Pipe Production:
Lightweight production equipment, low investment, rapid construction, simple welding method, a wide array of product specifications, high dimensional accuracy, minimal wall thickness deviation, smooth surface, and a high rate of finished products characterize the advantages of stainless steel welded tubes. In mass production scenarios, the cost of producing welded pipes is approximately 20% lower than that of seamless pipes. In recent years, a prevalent method in the country involves the 'welding-cold rolling' process for producing stainless steel tubes. This process entails cold-rolling (drawing out) slit and shaped cold-rolled coils according to specifications, followed by welding using multiple-gun argon arc welders. The weld's performance indicators closely match those of the parent metal, leading to significantly improved product quality. Consequently, the advantages of employing stainless steel welded tubes over stainless steel seamless tubes have become increasingly evident.
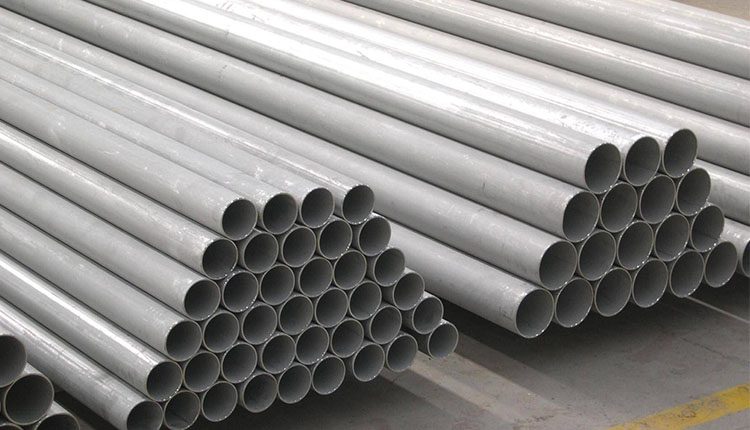
Benefits of Producing Stainless Steel Welded Pipes:
In the manufacturing of stainless steel welded pipes, the initial step involves the uniform extrusion of the pipe body. Subsequently, through online bright solid annealing, the surface achieves a remarkably smooth finish, rendering it resistant to scaling and featuring anti-fouling properties. This smooth surface not only aids in efficient heat dissipation but also reduces the need for frequent cleaning, saving time and effort. Additionally, as a deep-processed product of the plate, welded pipes boast an unparalleled advantage of uniform wall thickness and can be precisely fixed at desired lengths. Moreover, the inherent corrosion resistance of stainless steel ensures a prolonged and durable lifespan in practical use.
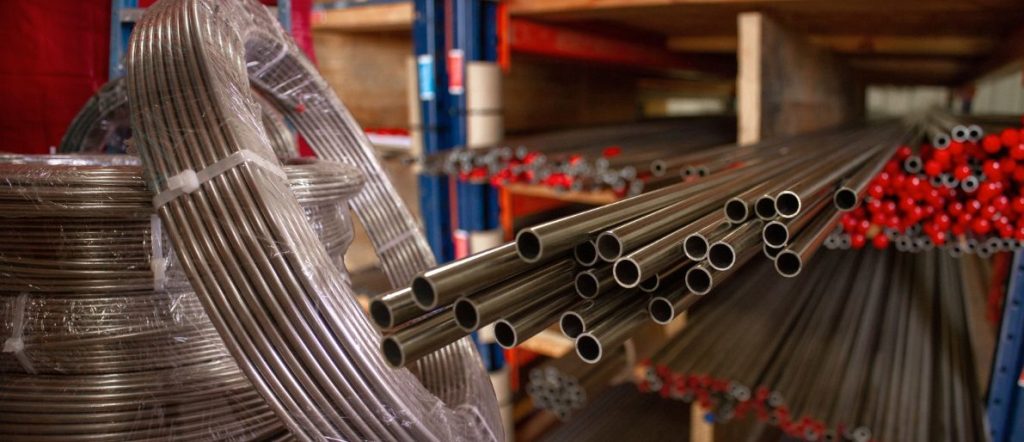
Current State of Stainless Steel Welded Pipe Offerings:
The production capacity of industrial-grade stainless steel welded pipes in China does not align with the domestic market demand. Many existing stainless steel welded pipe facilities lack essential equipment, including heat treatment and online testing capabilities, limiting their production capacity. Consequently, these units can typically only produce general decorative tubes, leading to an oversupply of medium-to-low-grade stainless steel decorative welded tubes. On the other hand, there is a significant shortage of production capacity for higher-standard industrial welded tubes, such as those used in chemical machinery and heat exchangers, with only a few manufacturers capable of meeting this demand.
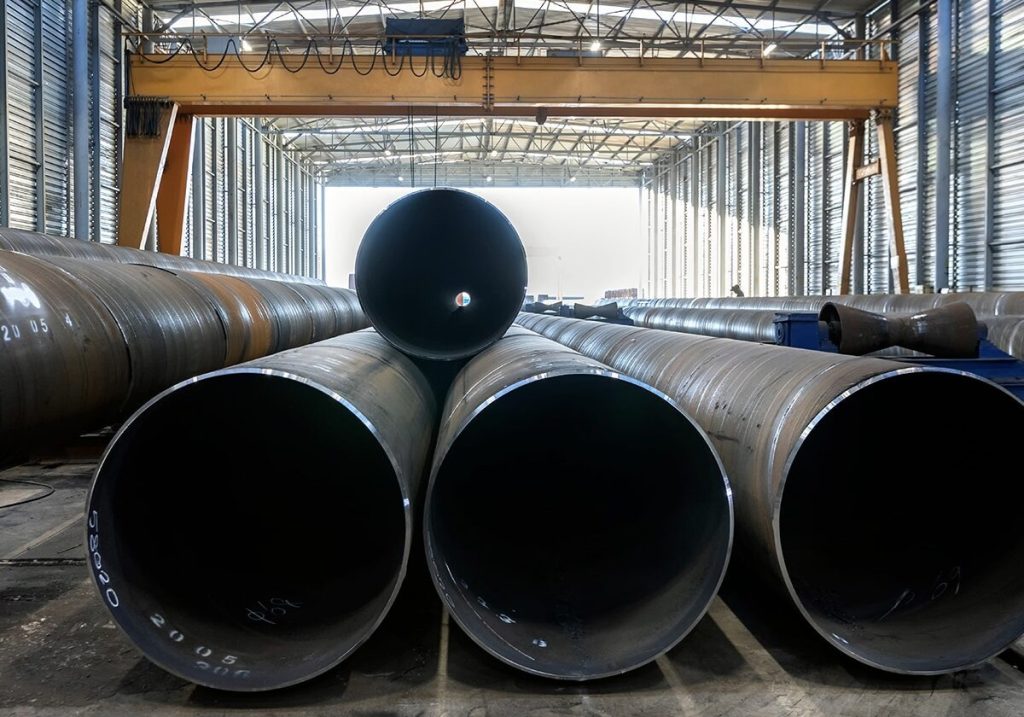
Chemical Composition of Stainless Steel Tubes:
Chemical composition | Element | 201 | 202 | 304 | 316 | S31803 | S32750 | |
C | ≤0.15 | ≤0.15 | ≤0.08 | ≤0.08 | ≤0.030 | ≤0.030 | ||
Si | ≤1.00 | ≤1.00 | ≤1.00 | ≤1.00 | ≤1.00 | ≤0.80 | ||
Mn | 5.5-7.5 | 7.5-10.0 | ≤2.00 | ≤2.00 | ≤2.00 | ≤1.20 | ||
P | ≤0.060 | ≤0.060 | ≤0.045 | ≤0.045 | ≤0.030 | ≤0.035 | ||
S | ≤0.030 | ≤0.030 | ≤0.030 | ≤0.030 | ≤0.020 | ≤0.020 | ||
Cr | 16-18 | 17-19 | 18-20 | 16-18 | 21-23 | 21-23 | ||
Ni | 3.5-5.5 | 4.0-6.0 | 42958 | 43022 | 4.5-6.5 | 6.0-8.0 | ||
Mo | 2.0-3.0 | 2.5-3.5 | 3.0-5.0 | |||||
N | ≤0.25 | ≤0.25 | 0.08-0.2 | 0.24-0.32 | ||||
Cu | ≤0.50 | |||||||
Mechanical properties | Material Item | 201 | 202 | 304 | 316 | S31803 | S32750 | |
Tensile Strength (MPa) | ≥655 | ≥620 | ≥515 | ≥515 | ≥620 | ≥800 | ||
Yield Strength (MPa) | ≥260 | ≥310 | ≥205 | ≥205 | ≥450 | ≥550 | ||
Elongation (%) | ≥35 | ≥35 | ≥35 | ≥35 | ≥25 | ≥15 | ||
Hardness (HV) | ≤230 | ≤230 | ≤200 | ≤200 | ≤303 | ≤323 |
Dimensions of Stainless Steel Tube Products:
Name | Stainless Steel tube |
Standard | ASTM A213,ASTM A312,ASTM A789,ASTM A790 |
Material Grade | 201/202/304/316/S31803/S32750 |
Outer Diameter | 0.1mm--219.1mm |
Thickness | 0.05mm - 20mm |
Length | ≤12000mm or as per customer request |
Tolerance | a) Outer Diameter: +/- 0.2mm |
b) Thickness: +/- 10% OR as customer request | |
c) Length: +/- 10mm | |
Surface | Satin / Hairline :180#, 320# |
Polish : 400# ,600# ,800# or Mirror surface | |
Pickling | |
Application | Decoration ,( Processed into railings, handrails, doors and Windows ),medical,industry,etc |
Packaing | Plastic bag/woven packing(please send details packing to us if you have other requirements) |
Is it Possible to Use Welded Pipes in Heat Exchange Equipment?
Achieving a higher standard product tube is feasible, and the heat exchanger tube plays an essential role in tubular heat exchanger equipment. Typically, the choice of heat exchanger tube depends on factors such as pressure and fluid medium. A common misconception in today's market is that stainless steel welded tubes cannot serve as heat exchanger tubes. However, GB/151-1999 clearly specifies that stainless steel welded tubes can be chosen when the tube pressure is ≤ 6.4 MPa. Notably, with the well-established production process of stainless steel welded pipes, they can effectively meet the requirements of general heat exchanger tubes, showcasing their distinct advantages.
Opting for the mature production process, welded pipes made of austenitic stainless steel stand as the preferred choice.
As the heat exchanger tube serves as the heat transfer surface, its size significantly impacts heat transfer efficiency. Utilizing a smaller diameter pipe results in a larger heat exchange area per unit volume, leading to more compact equipment, lower metal consumption per unit heat transfer area, and higher heat transfer coefficients. Despite potential manufacturing complexities, employing austenitic stainless steel welded pipes as heat exchanger tubes addresses these challenges. This choice is advantageous due to the stainless steel's excellent corrosion resistance, smooth surface, and mature production process, making it the preferred option for heat exchanger applications.