Boiler steel plate stands as a crucial material in the fabrication of boilers. Primarily, it encompasses hot-rolled special carbon steel and low-alloy steel, employed in the production of vital components like boiler shell, drum, header cover, and hanger. This material is specifically designed for its heat-resistant properties, making it suitable for medium and thick steel plate applications.
Boiler steel plates are frequently exposed to challenging conditions, characterized by medium to high temperatures and pressures. Beyond enduring elevated thermal and pressure stresses, these plates must also withstand impact, fatigue loads, and corrosion from water and gas, creating harsh working environments. The occurrence of a destructive accident in the boiler during operation can lead to significant damage.
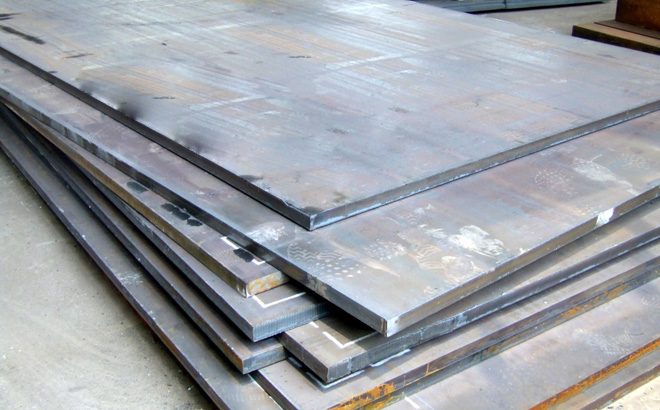
Hence, it is imperative for boiler steel plates to possess commendable physical and mechanical properties, as well as excellent processability. Stringent regulations outlined in the material standards' technical provisions are enforced to ensure the safety of their use.
Categorized by Material
From a material perspective, boiler steel plates can be categorized into two types: special carbon steel plates and low-alloy heat-resistant steel plates.
The materials used in boiler steel plates undergo stringent control over chemical composition, with a particular emphasis on regulating harmful elements such as phosphorus and sulfur, as well as residual elements like chromium, nickel, and copper. The smelting process ensures effective deoxidation and the removal of non-metallic inclusions to achieve desirable plasticity and toughness.
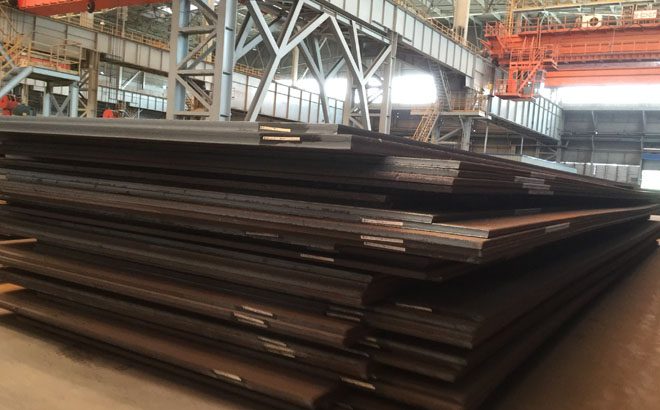
Uniform structure is a requirement, with grain size controlled within a specified range, typically between 3 and 7. Rigorous standards apply to surface quality and internal defects. Additionally, both normal temperature and high-temperature mechanical properties must meet stringent criteria.
According to the GB/T713-2014 standard titled 'Steel Plates for Boilers and Pressure Vessels,' it explicitly mandates the use of an oxygen converter or electric furnace for smelting, coupled with the requirement for refining treatment. Simultaneously, it emphasizes the necessity of maintaining a continuous casting billet during hot rolling, with a compression ratio not less than 3.
Categorized by Use
Boiler steel plates are categorized based on different operating conditions, distinguishing between plates designed for room temperature and medium temperature pressure parts and those engineered for high-temperature pressure components.
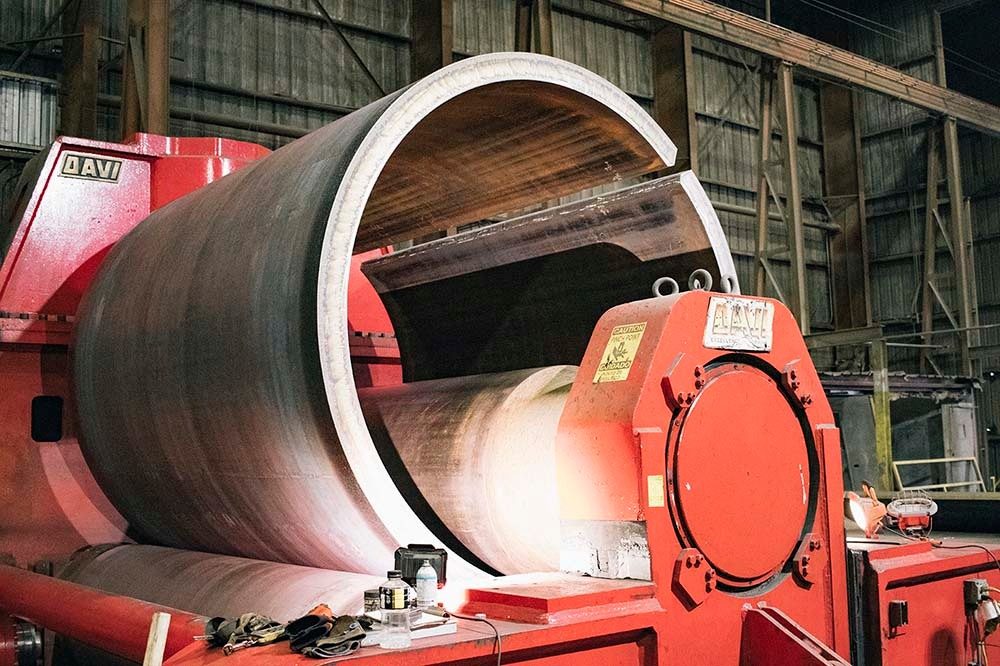
Steel plates for room temperature and medium temperature applications (below the creep temperature) are predominantly crafted from carbon steel. This includes various types such as carbon steel, carbon-manganese steel, and carbon-manganese-silicon steel. Examples include Q245R as per GB/T713-2014 "Steel for boilers and pressure vessels," Q345R (20g, 22Mng, 16Mng, 19Mng steel in GB/T713-1997 "Boiler Steel Sheet"), and ASME SA-515/SA-515M "Carbon Steel Sheet for Medium and High Temperature Pressure Vessels," SA-299/SA-299M "Carbon Manganese Silicon Steel Sheet for Pressure Vessels," among others. These plates are primarily employed in the manufacturing of boiler drums and pressure-receiving parts, such as tank end caps, for applications below medium temperature.
Boiler steels intended for room temperature and moderate temperature applications must possess
- Elevated strength at room temperature;
- Excellent impact toughness with low notch sensitivity;
- Effective aging toughness due to substantial cold deformation required for drum processing;
- Superior processability and weldability;
- Well-formed low-power structure, and more.
At elevated temperatures, especially beyond the creep threshold, boiler steel plates typically employ low-alloy heat-resistant steel. Commonly used varieties include chromium-molybdenum steel, chromium-molybdenum-vanadium steel, and chromium-molybdenum-tungsten steel. These steels are primarily utilized in the fabrication of high-temperature pressure-bearing components such as end caps for high-temperature headers and blocking plates for steam pipes.
For instance, GB125-2014 specifies boiler steel plates like 15CrMoR and 12Cr1MoVR, while the US ASME SA-387/SA387 M includes chromium-molybdenum alloy steel plates for pressure vessels, such as Gr22 and Gr91. Additionally, ASME SA1017/SA1017M outlines pressure vessel specifications for chromium-molybdenum-tungsten alloy steel plates, including Gr23, Gr911, Gr122, and others.
Boiler steel plates designed for elevated temperatures must possess:
- Effective resistance to high temperatures and enduring plasticity;
- Stable structure at elevated temperatures;
- Resilient against oxidation at high temperatures (heat resistance);
- Excellent capabilities for both hot and cold processing, particularly in terms of cold bending deformation and weldability.
Key Characteristics of Boiler Steel Plate
Given the crucial role of boiler steel plates and the stringent safety and reliability requirements, the manufacturing process is intricate. Consequently, the materials must exhibit the following key characteristics:
- High yield strength performance within a specific temperature range, especially at medium and high temperatures.
- Adequate toughness to prevent brittle failure during both manufacturing and usage.
- Low sensitivity to strain aging, particularly within the relevant working temperature range, ensuring a consistent value of aging impact work.
- Minimal notch sensitivity to prevent steel from cracking in welding, openings, and areas of local stress concentration.
- Favorable welding properties for ease of fabrication.
- A sound microstructure with no tolerance for white spots or cracks.
Primary Manufacturing Steps for Boiler Steel Plates
Given the essential characteristics of the aforementioned boiler steel plates, precise control over composition, minimal impurity elements, employment of pure steel smelting technology, and meticulous temperature control are imperative during the production process. This necessitates the utilization of advanced production technologies. In China, the widespread adoption of cutting-edge equipment and advanced production techniques has facilitated the widespread use of high-quality boiler steel plates.
Typically, in the modern wide and heavy plate production line, the production of steel sheets for boilers involves the following processes:
- Hot metal desulfurization pretreatment
- Smelting production of converter clean steel
- Furnace refining to eliminate non-metallic inclusions
- RH cycle deep degassing process, significantly reducing hydrogen, oxygen, nitrogen, and other gas content while maintaining stable molten steel temperature
- Implementation of advanced defect-free slab casting technology to produce high-quality slabs
- Application of controlled rolling and controlled cooling to ensure a uniform structure and grain
- Precise control over heat treatment temperature
With the increasing demand from large-scale power stations, a considerable number of subcritical, supercritical, and even ultra-supercritical boilers have been deployed in industrial applications. Consequently, there has been substantial development in boiler steel plates as fundamental materials.